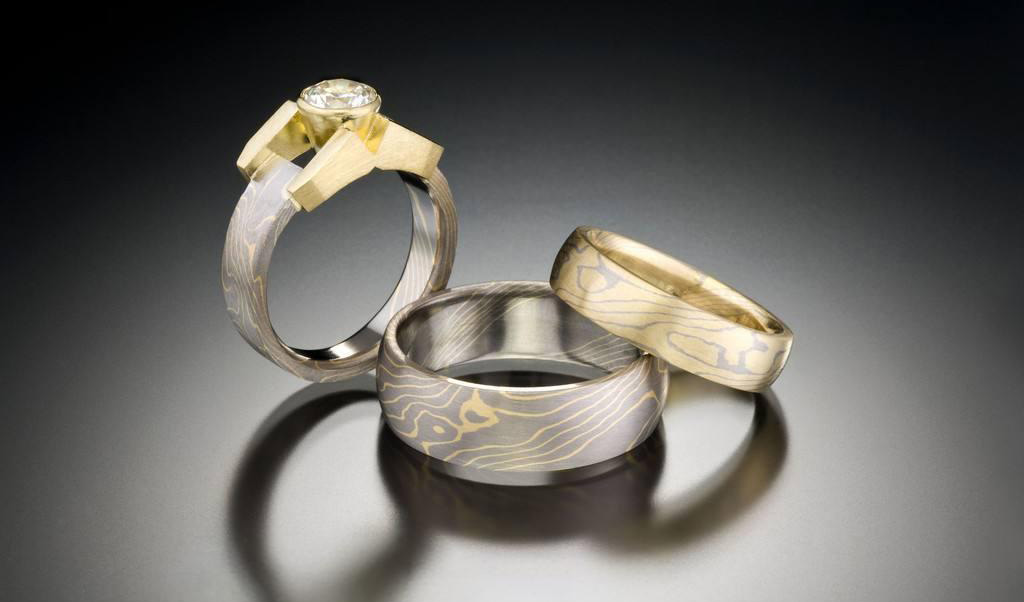
Choosing the right welding method
Precisely control welding parameters: Before welding, it is necessary to carefully analyze and determine process parameters such as welding speed, power, laser beam diameter, etc. Avoid damage to jewelry caused by excessive temperature and welding time, and also reduce thermal stress and heat-affected zone generated during welding, so as to maintain the original texture and shape of the jewelry.
Use appropriate welding technology: According to the material and fracture condition of the jewelry, the appropriate welding technology should be selected. For example, for precious metal jewelry such as gold, high-precision welding methods such as laser welding and tungsten inert gas welding can be used, which can provide more delicate welding effects and smaller heat-affected zones.
Use appropriate solder and auxiliary materials
Choose solder that matches the material of the jewelry: The choice of solder should match the material of the jewelry to ensure the welding effect and firmness. At the same time, the color, gloss and other characteristics of the solder should also be similar to the jewelry to avoid problems such as inconsistent color and gloss after welding.
Use auxiliary materials: During the welding process, auxiliary materials such as borax can be used to clean and assist the welding to remove oxides and impurities on the surface of the jewelry and improve the welding quality and effect.
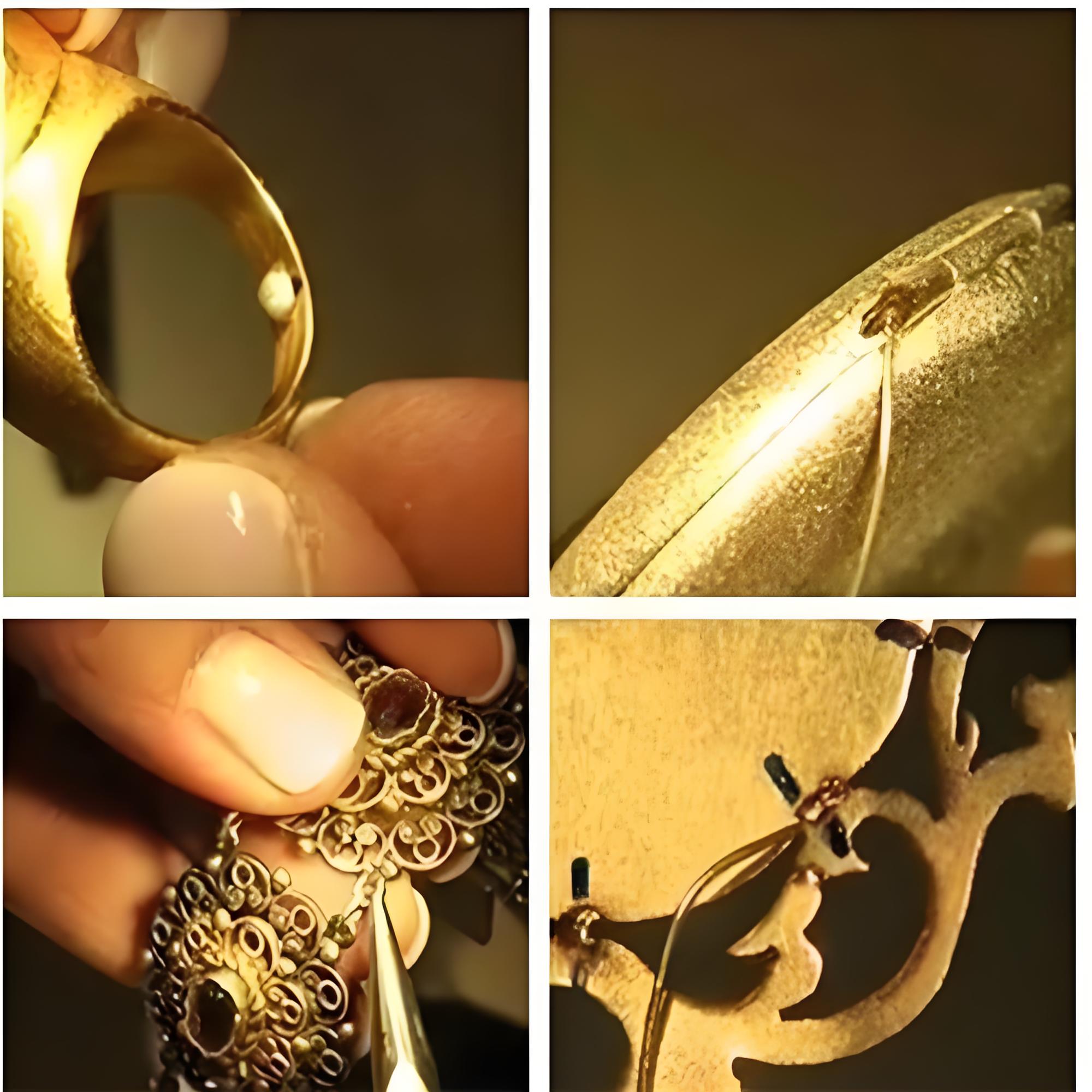
Delicate welding operation
Preheating and cooling: Properly preheating the jewelry and solder before soldering will help the solder melt better and combine with the jewelry material. Cool slowly after soldering to avoid deformation caused by rapid cooling.
Control the soldering position: Try to choose the soldering position in a hidden or inconspicuous part of the jewelry to reduce the impact on the overall texture.
Keep the soldering flat: During the soldering process, keep the soldering flat and even to avoid unevenness or solder accumulation.
Detailed follow-up processing
Shaping and polishing: After welding, the weld needs to be finely shaped and polished to remove excess solder and uneven parts, so as to restore the original shape and texture of the jewelry.
Polishing: Polish the weld to restore its original gloss and texture. Pay attention to uniformity and meticulousness during the polishing process to avoid inconsistent gloss.
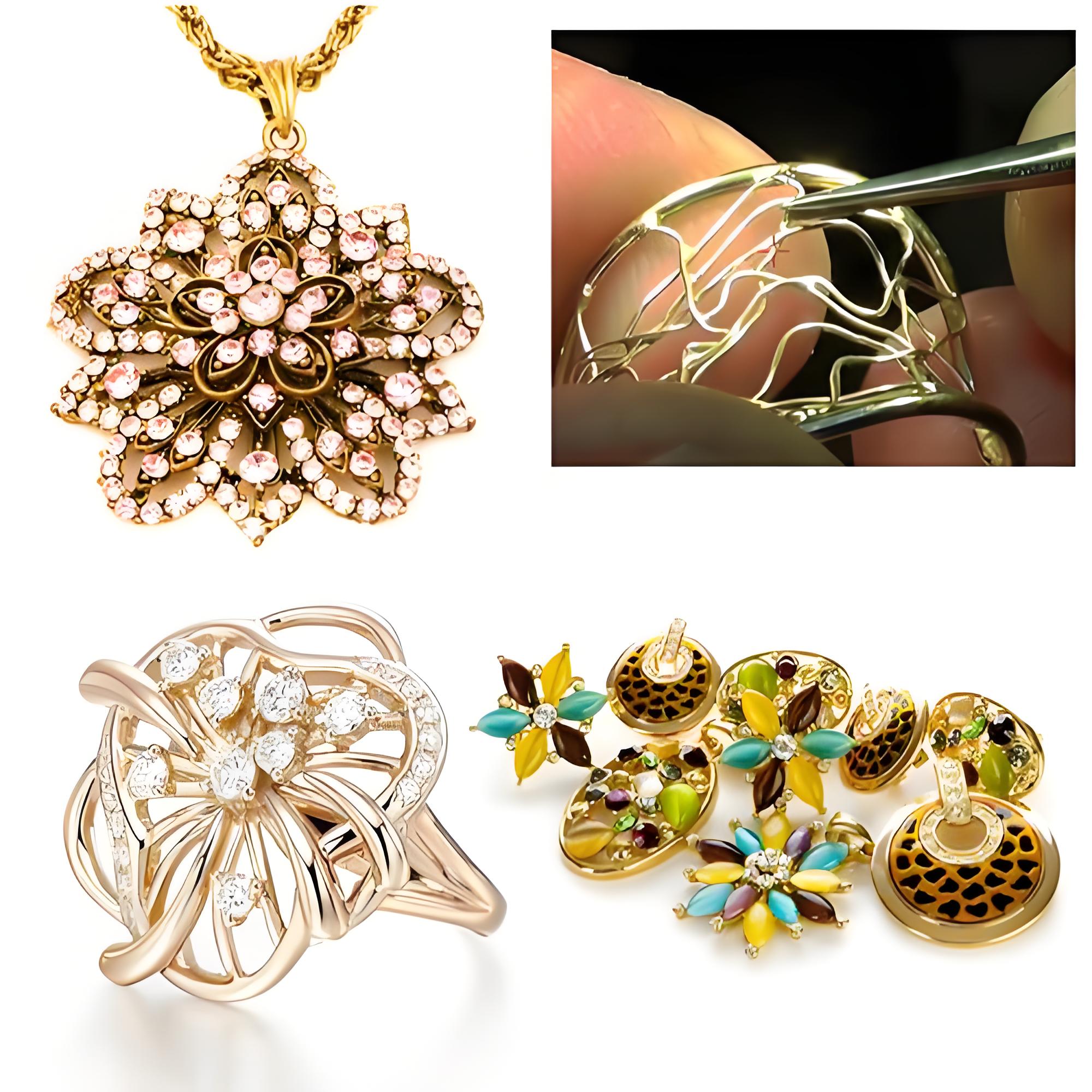
Dowin Laser specializes in the production of various types of laser welding machines, and can quickly help customers choose the right jewelry welding machine. At the same time, we also support customized laser equipment, provide customers with free design solutions and technical support, and help customers start welding work as soon as possible. Contact us and get your jewelry laser welding machine now!
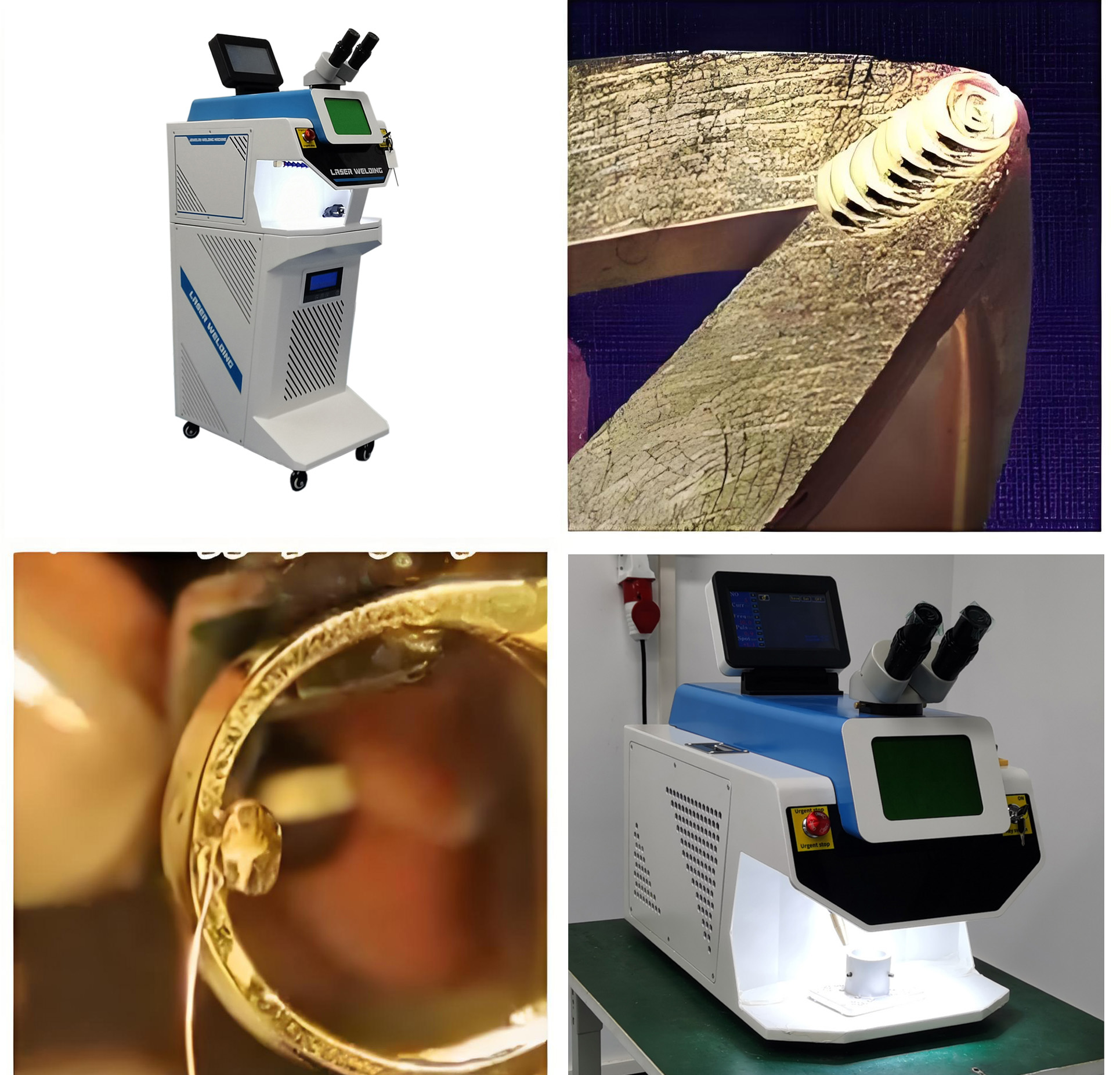
Post time: Jul-24-2024