mould laser welding machines
Looking for a mold repair laser welding machine for metal? Check out our 3 models, Can quickly and accurately repair the pores, slag holes, and shrinkage holes formed during the casting process.Suitable materials for laser repair include ductile iron, gray iron, stainless steel, etc.
Here's Why It's Awesome
Fiber laser and QCW laser can be selected, with stable and reliable beams. Equipped with a dedicated chiller, which can meet long-term welding requirements and provide better stability.
Fiber laser and QCW laser can be selected, with stable and reliable beams. Equipped with a dedicated chiller, which can meet long-term welding requirements and provide better stability.
Configurations:
Automatic YAG laser welding machines is widely used in high precision mobile phone batteries, sensors, medical devices, craft gifts, clocks, electronic components, sensors, precision machinery, communications and other industries
Configurations:
YAG Mold repair laser welding machine with yag spot laser welding, strong point energy, focused on all kinds of plastic injection mold, car precision mold etc., cracks, chippings, edges and corners, sand holes and mold wear etc repair.
Configurations:
YAG Mold repair laser welding machine with yag spot laser welding, strong point energy, focused on all kinds of plastic injection mold, car precision mold etc., cracks, chippings, edges and corners, sand holes and mold wear etc repair.
Configurations:
crane arm laser welding machine with unique structure design, it is suitable for repairing of large (size Max Diameter is 3000mm around), medium and small molds. with lifter arm, free to move to meet the repair needs of variety of mold materials
Application materials
-Can be used on titanium, nickel, tin, zinc, copper, aluminum, chromium, niobium, gold, silver and other metals and their alloys, as well as steel.
-Welding of the same material of such alloys as felling alloys may also be applied to copper-Nickel, nickel-titanium, copper-titanium, brass-copper.
-Low carbon steel – copper and other heterogeneous metal welding.
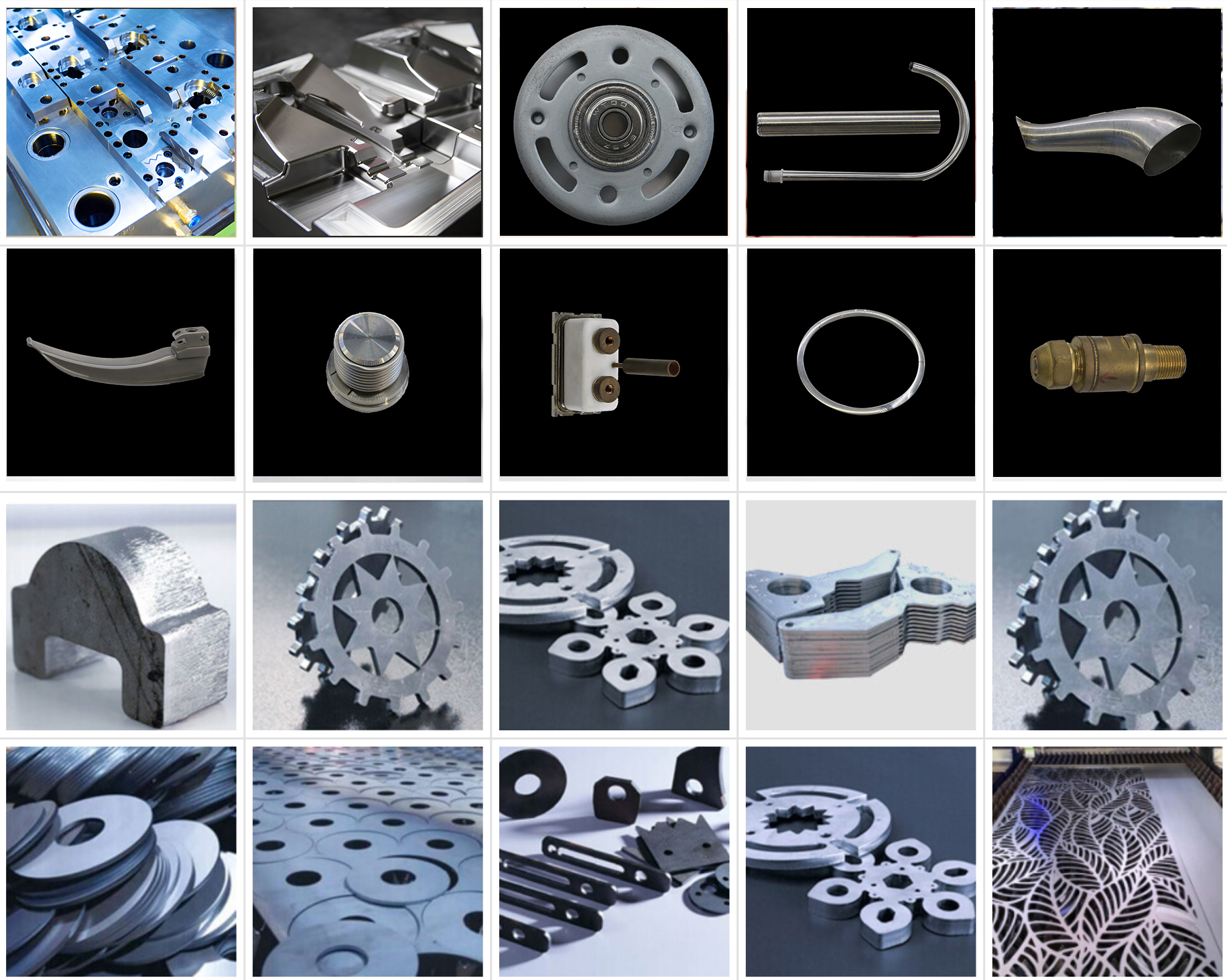
Advantages of Mould Laser Welding Machines
-
High Precision:
- Laser welding offers extremely high precision, suitable for intricate shapes and small components.
-
Minimal Heat Impact:
- The process has low heat input, resulting in a small heat-affected zone, which reduces material deformation and stress.
-
High Welding Quality:
- Produces smooth welds without pores, with high welding strength, often eliminating the need for further processing.
-
Material Compatibility:
- Capable of welding a variety of metals, including those difficult to weld with traditional methods.
-
High Flexibility:
- Suitable for welding complex shapes and components, and easily integrated with automation and multi-axis systems.
-
High Efficiency:
- Fast welding speeds significantly reduce processing time and increase production efficiency.
-
Non-Contact Processing:
- No need to contact the workpiece, reducing mechanical stress and wear.
-
Environmentally Friendly:
- Produces no slag or smoke emissions, minimizing environmental pollution.